In the processing industry, sheet metal processing has become a more prominent and common processing form, and sheet metal products are more and more popular with users, such as lockers, workbenches, shelves, sheet metal cabinets, etc., from the previous plastic To sheet metal production, it increases the strength of the user and prolongs the service life.
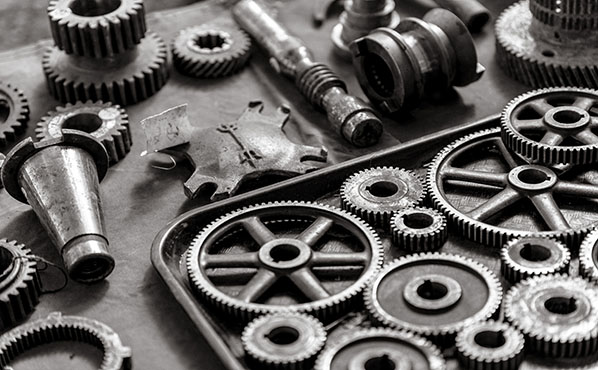
Sheet metal processing can be divided into ordinary processing and precision processing. For normal sheet metal finished products, the difference is the accuracy required to machine the item. For example, some daily occupancy items can meet process requirements through common machining standards. Precision sheet metal is mainly used in industries with special assembly requirements or high appearance requirements. Let's talk some common sense about sheet metal.
In the processing industry, sheet metal processing has become a common processing form, and sheet metal products are more and more popular with users, such as shelves, workbenches, shelves, sheet metal cabinets, etc. From the previous plastic to sheet metal production, it can be Improve the user's strength and prolong the service life.
Sheet metal processing can be divided into general processing and precision processing. For general sheet metal finished products, the difference lies in the precision requirements of the processing items. For example, for some daily busy ordinary projects, general processing standards can meet the process requirements. Sheet metal accuracy is very important for industries with special assembly requirements or high demands. Here is some common sense about sheet metal.
Sheet metal processing includes traditional cutting, slitting and bending methods and process parameters, including various cold forming structures and process parameters, various working principles and equipment operation methods, as well as new stamping technologies and new processes. The processing of sheet metal parts is called sheet metal processing.
After obtaining the drawings, select different blanking methods for different openings and batches, including laser, CNC drilling, cutting and casting, and then open the drawings accordingly. Placing the worktable next to the CNC and the laser facilitates the placement of the plate on the machine for processing and reduces the workload of lifting the plate. Some of the available edge material is placed in designated places to provide material for die testing while bending. After the workpiece is blanked, it is necessary to repair the corners, burrs and joints (grinding treatment). Use a flat file to repair the tool joint, use a grinder to repair the workpiece with large burr, and use the corresponding small file to repair the small inner hole joint to ensure a beautiful appearance. At the same time, the repair of the appearance also ensures the positioning during bending, so that the position of the workpiece on the bending machine is consistent, and the consistency of the size of the same batch of products is guaranteed.
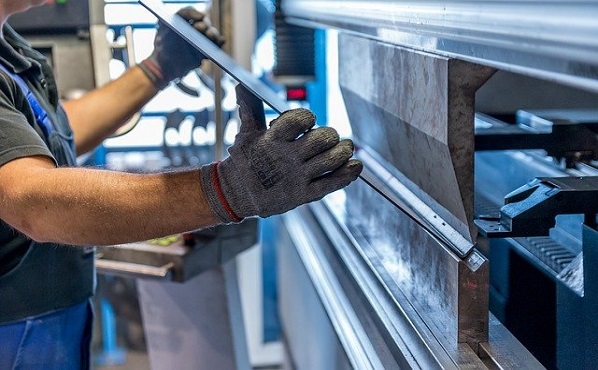
Commonly used materials are galvanized steel sheet, cold-rolled sheet, hot-dip galvanized steel sheet, and stainless steel. 1. Galvanized steel sheet is electro-galvanized sheet. 2. Cold-rolled sheet refers to the continuous rolling of steel ingots into steel sheets. 3. Hot-dip galvanized steel sheet refers to the sheet that is plated with zinc layer after hot-rolled pickling or cold-rolling.
The above is the little knowledge of sheet metal processing. Do you want to know more about sheet metal processing? Platinum Shield will continue to give you more knowledge about sheet metal processing.