There are four main types of laser cutting.
fusion cutting
In laser fusion cutting, the workpiece is partially melted and the melted material is ejected by means of an air jet. Since the transfer of the material takes place only in the liquid state, the process is called laser fusion cutting. In laser fusion cutting, the material is of course heated to a certain temperature and melted, and then a non-oxidizing gas is blown out through a nozzle coaxial with the beam, and the pressure of the gas is used to discharge the liquid metal and form a cut. Laser fusion cutting only requires 1/10 the energy of steam cutting, and does not require complete vaporization of the metal. Laser melting cutting can produce no oxidation in ferrous materials and titanium alloys. For steel materials, the laser power density for melting rather than gasification is between 104W/cm² and 105W/cm².
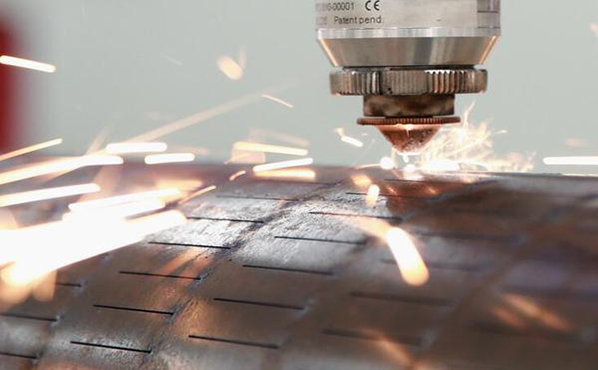
Vaporization cutting
The laser vaporization cutting process uses a high-energy, high-density laser beam to heat the workpiece, raise the temperature, and vaporize the material into steam in a very short period of time. cut. However, the heat of vaporization is usually so great that the surface temperature of the material rises rapidly to the boiling temperature, avoiding melting due to heat conduction, so part of the material vaporizes and disappears as a vapor, and part of the material is ejected from the auxiliary gas stream as a jet The cut bottom is blown away. In this case, very high laser powers are required. To prevent material vapor from condensing on the cutting wall, the thickness of the material should not greatly exceed the diameter of the laser beam. Therefore, this process is only suitable for applications where exclusion of molten material must be avoided. The materials used for laser vaporization cutting are generally very thin metal materials and non-metal materials. Under a certain sheet thickness, the maximum cutting speed is inversely proportional to the vaporization temperature of the material. The required laser power density is above 108W/cm², depending on the material, the depth of cut and the position of the beam focus. Oxidation melting cutting (laser flame cutting)
Fusion cutting generally uses inert gas. If oxygen or other reactive gas is used instead, the material will be ignited by the laser beam, and a violent chemical reaction with oxygen will generate another heat source, thereby further heating the material, which is called oxidative fusion cutting. Due to this effect, for the same thickness of structural steel, a higher cutting rate than fusion cutting can be obtained with this method. On the other hand, the cut quality of this method may be worse compared to fusion cutting. In fact, it produces wider cuts, pronounced roughness, increased heat-affected zone, and poorer edge quality. Laser flame cutting is not ideal when dealing with delicate models and sharp corners (risk of burning the sharp corners).
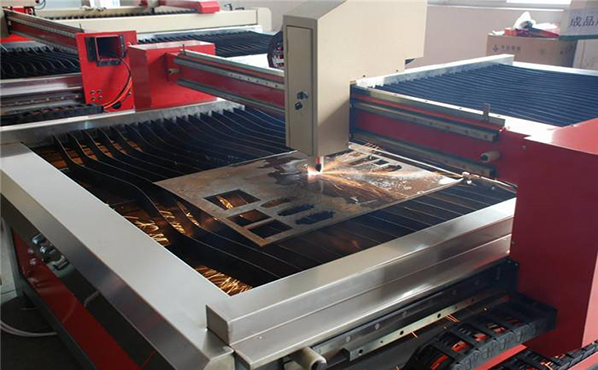
controlled fracture cutting
For brittle materials susceptible to thermal damage, high-speed, controlled cutting by laser beam heating is called controlled fracture cutting. The main content of this cutting process is that if a small area of a brittle material is heated by a laser beam, it will cause a large thermal gradient and strong mechanical deformation in that area, resulting in the formation of cracks in the material. The reliable way is that the laser beam can guide the crack in any desired direction as long as a balanced heating gradient is maintained. Materials typically used for this type of cutting are brittle materials.
The above are the 4 cutting methods of laser cutting.