Sheet metal processing involves many processing technology fields, such as material, bending, welding and so on. These are just one of the processes, so what are the names of the other processes?
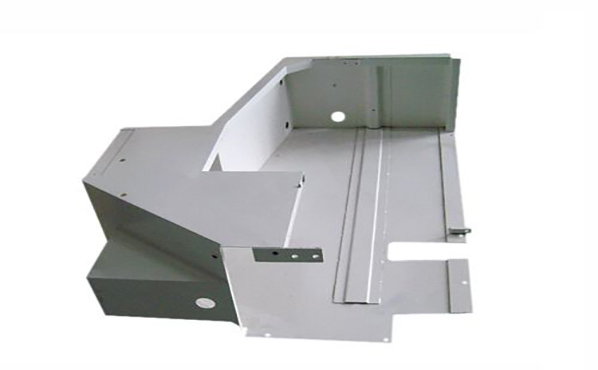
Platinum shield sheet metal processing tells you "
1. Shearing: refers to the process of obtaining a rectangular workpiece from a plate through a shearing machine.
2. Digital punching: refers to the punching operation with a CNC punching machine. It is necessary to program and process the surface of the digital punching diagram as the direction of the production front of the part. Process the quantity enough.
3. Laser cutting: refers to the process in which the workpiece is unloaded by the laser cutting machine
4. Cutting machine cutting: refers to a process of cutting material with an electric grinding wheel cutting machine. This process has certain processing safety risks, and process engineers should use this process less.
5. Saw material: refers to a process of cutting material with a sawing machine. This is not demanding, and it is mostly cutting material for profiles.
6. Blanking: refers to the process of obtaining the shape of the product by using a mold on an ordinary punch or other equipment.
7. Punching: refers to the process in which the workpiece is machined by ordinary punching machines and molds.
8. Bending: refers to the process in which the workpiece is formed by the bending machine. Our company refers to the use of CNC bending machines and corresponding bending dies, and the first test machine, machine adjustment, and first inspection can be produced before production.
9. Punching and folding: It refers to the use of ordinary punching machines to install special molds for the bending of small and simple workpieces.
10. Forming: refers to the process of deforming the workpiece by using a mold on an ordinary punch or other equipment.
11. Hole drawing: also known as "flanging", which refers to the process of using a die to form a round hole on the workpiece on an ordinary punch or other equipment.
12. Drilling: refers to the drilling operation with a drilling machine. When several punching and general punching are inconvenient for processing, a small amount of manual processing is performed. Normally, the method of scribing is used to add punching points to locate drilling. The process engineer must Use this technique sparingly.
13. Die plate drilling: refers to first processing a template with a number of punches, and then using the positioning method to perform batch drilling.
14. Tapping: refers to the process of machining internal threads on the workpiece.
15. Hole reaming: refers to the process of processing small holes on the workpiece into large holes with drills or milling cutters.
16. Countersunk hole: refers to the process of machining a taper hole on the workpiece in order to match the connector like a countersunk head screw.
17. Pressure riveting: refers to the process of firmly crimping fasteners such as pressure riveting nuts, pressure riveting screws or pressure riveting nut columns on the workpiece by using a punch or hydraulic press. Normally, the direction of loading the pressure riveting parts is the burr direction, so that the pressure riveting parts can be loaded smoothly. If not, the manufacturer should report it in time.
18. Riveting: refers to the process of first countersinking the workpiece, and then using a punch or hydraulic press to firmly crimp the rivet nut on the workpiece.
19. Pull mother: refers to a process similar to riveting. The process of firmly connecting connectors such as rivet nuts (POP) to the workpiece with a pull mother gun.
20. Pull riveting: refers to the process of tightly connecting two or more workpieces with pull rivets using pull rivet guns as tools.
21. Riveting: The process of connecting two or more workpieces face-to-face with rivets. For countersunk riveting, the workpieces need to be countersunk first.
22. Punching and convex hull: refers to the process of forming a convex shape on the workpiece with a die on a punch or hydraulic press.
23. Punching and tearing: also known as "punch bridge", which refers to the process of forming a workpiece into a bridge-like shape with a die on a punch or hydraulic press.
24. Imprinting: refers to the process of using a mold to punch out characters, symbols or other imprints on the workpiece.
25. Corner cutting: refers to the process of cutting off the corner of the workpiece using a die on a punch or hydraulic press.
26. Punching mesh holes: refers to punching out mesh holes on the workpiece with a die on an ordinary punch or a CNC punch.
27. Flattening: refers to the process of transitioning a workpiece with a certain shape to a flat.
It is a common term for sheet metal processing.