Let's first understand the classification of sheet metal processing technology. Sheet metal processing chooses different processing blanking methods according to different processing requirements, including laser cutting, CNC plasma cutting, shearing machine processing and other different methods. Generally, sheet metal processing manufacturers In order to consider the cost, most of them are cut with a scissor. However, for some precision requirements and to ensure processing efficiency, taking Jianzheng Machinery as an example, CNC laser cutting machines are usually used.
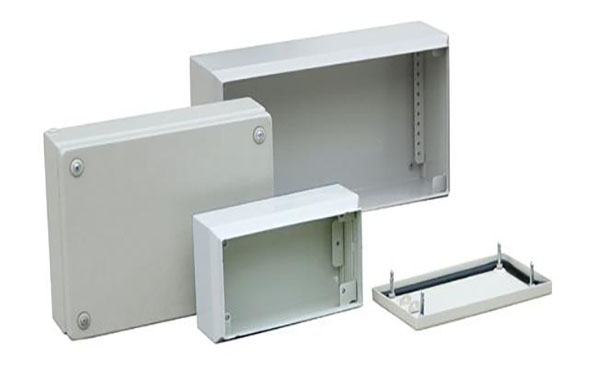
We can see what equipment we need through the sheet metal processing process. The four most important steps in the sheet metal process are shearing, punching/cutting/, folding/rolling, and welding.
The first step is to cut the plate to the corresponding size. The required equipment is a plate shearing machine or a laser cutting machine. The traditional plate shearing machine can only cut the plate. Now the laser cutting technology is mature, and the laser cutting machine is used to cut the plate. The laser cutting precision is high, the automation flexibility is strong, and the applicable material range is wide. There is no limit to the shape and size that can be cut.
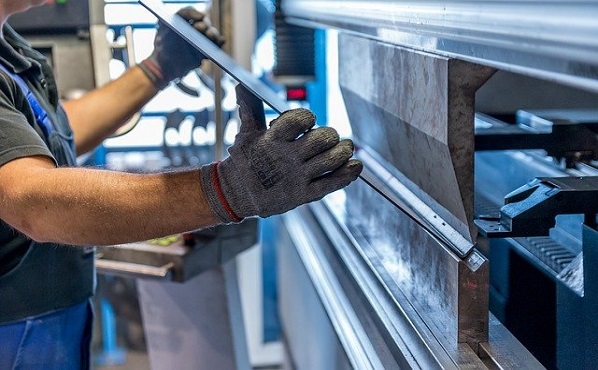
The second step is punching/cutting, punching, deep drawing and riveting of the sheet, the required equipment is a press, a riveting machine, etc.
The third step is folding/rolling, bending and hemming the sheet, and the required equipment includes bending machine, rounding machine and so on. Now in addition to the traditional manual press brakes, there are also automatic press brakes and robotic arms. The fourth step is welding, splicing the plates to form sheet metal parts, and the required equipment is arc welding machine, resistance welding machine, butt welding machine or robotic arm.
Sheet metal processing equipment summarizes the above points. Want to learn more about sheet metal processing? Bolden will continue to give you more knowledge about sheet metal processing.