How to improve the production efficiency of sheet metal parts during sheet metal processing.
1. Stainless steel is mainly used without any surface treatment, and the cost is high.
2. Hot rolled sheet SHCC, material t≥ 3.0mm, is also electroplated and painted parts, low cost but difficult to form, mainly flat parts.
3. Galvanized sheet SECC, State Grid Corporation of China. SECC electrolytic plate is divided into n material and p material. The N material is mainly not subjected to surface treatment, and the cost is high. P material is used to paint parts.
4. Copper is mainly made of conductive materials, and the surface treatment is nickel plating, chrome plating or no treatment, which is costly.
5. Aluminum sheet; usually using surface chromate (j11-a) and Suzhou laser sheet metal processing oxidation (conductive oxidation and chemical oxidation). Costs are high, including silver and nickel plating.
6. Aluminum profiles; materials with complex cross-sectional structures are widely used in various plug-in boxes. Surface treatment with aluminum plate.
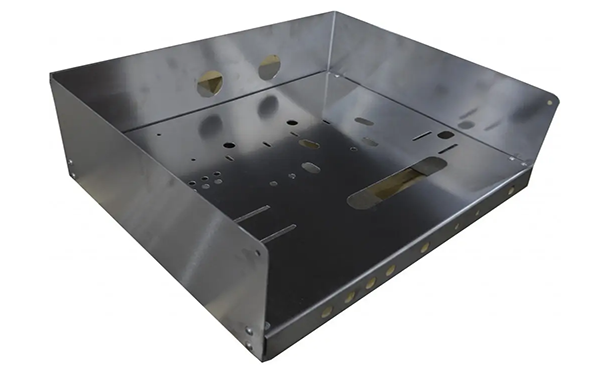
7. same. Cold-rolled sheet SPCC is mainly used for electroplating and baking paint parts, with low cost, easy forming, and large material thickness ≤ 3.2 mm. Usually, the 90-degree bend in sheet metal processing needs to be achieved by the pressure in the V-groove, so the relationship between them is the relationship between the tool and the tool. V-groove processing can also be said to be a sheet metal processing process. After some sheet metal products (thick material) are bent, the outer R angle is too large and unsightly, so a V-shaped groove is planed at the bending position (that is, the thickness of the sheet becomes thinner). The V-groove has two functions: one is to reduce the curved fillet. In general, the curved fillet of the sheet is equal to the thickness of the sheet. If the bending inner circle angle required by the workpiece is smaller than the plate thickness, the V-groove needs to be planed; the second is to reduce the bending force. In Suzhou sheet metal processing plant, when the bending force of the workpiece is greater than the tonnage of the bending machine and cannot be bent, a V-shaped groove can be planed to reduce the bending force.
1. Blanking: There are various methods of blanking, mainly the following methods
① Punching machine: After unfolding the parts on the flat plate one or more steps, punch out the flat parts with a punching machine to form materials of various shapes. Its advantages are short working time, high efficiency, high precision and low cost. It is suitable for mass production, but the mold should be designed.
② Cutting machine: for cutting simple strips. Mainly used for processing preparation for die blanking. The cost is low and the accuracy is less than 0.2, but it can only process strips or blocks without holes and corners.
③ Laser punching is to cut the structural shape of the flat plate on the large flat plate by the method of laser cutting. Like CNC blanking, it requires writing a laser program. It can cut flat parts of various complex shapes with high cost and an accuracy of 0.1.
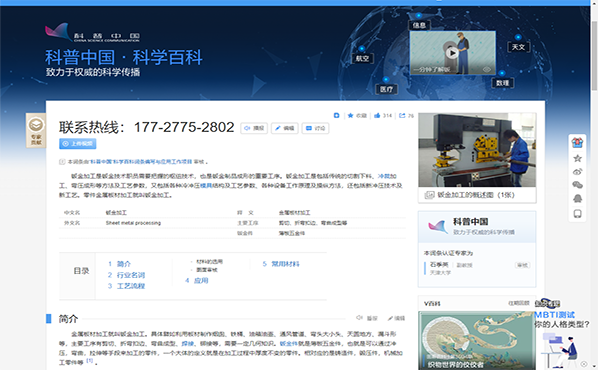
④ CNC punching. When CNC blanking, first write the CNC machining program, and use the programming software to write the drawn unfolding into the program that the CNC digital drawing processing machine can recognize, so that it can process the sheet metal parts step by step according to these programs, and put them on the flat plate. Stamping flat parts of various structural shapes. However, its structure is affected by the tool structure, the cost is low, and the accuracy is 0.15.
⑤ Sawing machine: mainly use aluminum profile, square tube, wire drawing tube, round steel, etc., with low cost and low precision. In the processing of many sheet metal parts, the assembly of sheet metal cabinets is very important, and its manufacturing process requirements are also very strict. The packaging containers of outbound goods must undergo performance inspection. When applying for inspection, the "Application Form for Inspection of Outbound Cargo Transport Packaging" and the inspection results of the batch of packaging containers of the production unit should be provided.