1. Cutting speed The laser head of laser cutting can move along the shape of the part per unit time. The higher the laser cutting speed and the shorter the cutting time, the higher the production efficiency of laser cutting. However, when other parameters are fixed, there is no linear relationship between laser cutting speed and cutting quality. A moderate cutting speed is a numerical range within which the energy of the laser beam stays on the surface of the part for too long, forming too many scorch marks. Completely melted, making it impossible to cut.
2. Laser output power. Laser power refers to the output energy of a laser system, while laser cutting refers to the ability of a laser beam to melt a material per unit of time.
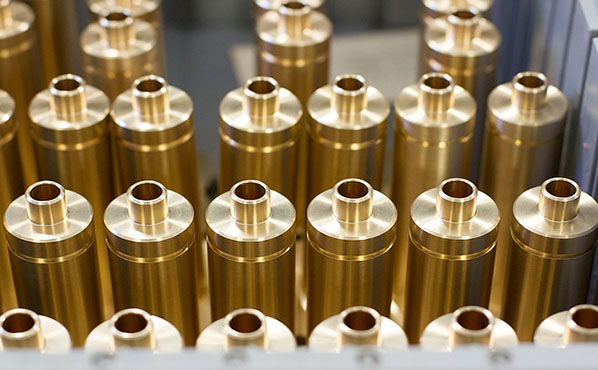
The laser output is finally focused by a special lens to where the power density is highest. The diameter of the focused beam is proportional to the depth of focus of the focusing lens. The focus of laser cutting is set according to the thickness, and different places have different thicknesses. Correct focus position is an important condition to obtain stable cutting quality. The cutting quality of laser cutting is not only related to the laser beam, but also to the characteristics of the laser beam focusing system, that is, the size of the laser beam after laser cutting focuses has a great influence on the laser cutting quality.
4. Auxiliary gas air pressure. Make a cut in the gap. Proper air pressure will speed up laser cutting. The size of the auxiliary gas pressure also affects the cutting efficiency of the fiber laser cutting machine. If the thickness of the material being cut by the laser increases or the cutting speed slows down, the gas pressure needs to be appropriately reduced. Cutting at lower gas pressure will reduce the risk of frost forming.
5. Nozzle distance The focused laser beam is irradiated to the surface of the part through a copper nozzle. The distance between the workpiece and the laser nozzle is called the nozzle distance. The distance from the nozzle to the part is measured in flow rate and pressure. If the distance is too far, the blowing power loss will be too large, and the exhaust gas flow rate will be too high, which will affect the scattering effect. A suitable distance is between 0.8 and 1.0 mm; the choice of nozzle type depends on the thickness of the material.
The system functions mainly include 3D visualization module of virtual processing scene, multi-platform machine tool kinematics calculation module, process implementation example and code output module. The 3D visualization module of virtual machining scene includes virtual machining scene construction, motion model construction and material removal process simulation. The multi-platform machine tool kinematics calculation module includes the kinematics calculation of the gantry 5-axis machine tool, the kinematics calculation of the vertical 6-axis robot and the reverse robot, and the calculation of the P matrix based on the tool position point. Process realization and code output modules include process defect display, collision detection implementation and transition trajectory display. Since a laser cut scene involves a wide range of models, it is necessary to quickly determine how to build the virtual environment. Due to the differences in the structure and operation mode of different machine tool platforms, point data is used to calculate the motion of the machine tool, and the results are input into the motion model to simulate the motion of the machine tool. In order to reflect the cut quality in the real-time cut marks, it is necessary to simulate the removal process of laser cut material. The phenomenon in the process of reflection and processing is simulated, and finally reliable processing code is generated for the corresponding platform.