Sheet metal parts are gradually being used for shelves and structural parts of food machinery, which is becoming a trend in the industry due to its open shape, simple manufacturing process and high manufacturing efficiency. Sheet metal is widely used in this field, but medium and thick plates are greatly affected by material thickness, bending process, welding process, etc. After forming, there is usually a relatively large gap, resulting in increased subsequent welding deformation, so the parts cannot be guaranteed. The size and shape tolerances, and even welding defects have a fatal impact on the appearance quality of the product.
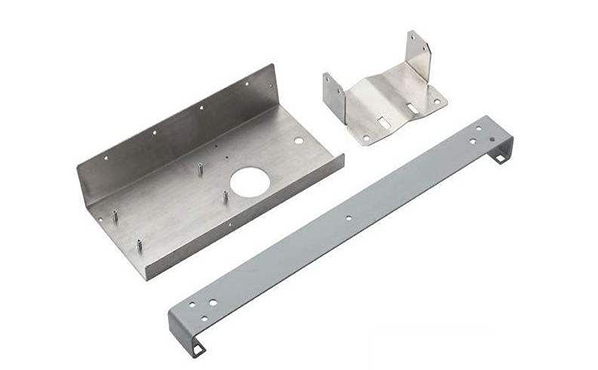
Part quality requirements
(1) First of all, ensuring the flatness of the reference plane A and the perpendicularity of the plane A and the planes B1 and B2 are the keys to satisfying the shape relationship of the assembly and ensuring the positional accuracy of the machine tool.
(2) To emphasize the bending accuracy, it is necessary to ensure the lateral dimensions of the faces B1 and B2 and the relative dimensions implied by the fixed support, as well as the dimensional accuracy relationship of the product.
(3) 形状精度和尺寸精度与下料、整平、折弯和焊接工艺密切相关。
sheet metal process
(1) The control of the sheet metal processing process should first emphasize the correctness of the process. The reasonable sheet metal processing process for this part is: raw material (drawn sheet metal with good flatness) → laser cutting → leveling → bending process (key process control) → welding.
(2) The second step is welding deformation control to ensure the accuracy of the parts.
1) The traditional process is to use the SolidWorks drawing method, normal laying out, bending, and welding. It turns out that the gap between the parts is very large, and the amount of wire filling is large during welding. Everyone knows that the deformation of stainless steel after welding will be relatively large, which will lead to parts. The deformation after welding cannot be controlled, and it is impossible to produce qualified products that meet the assembly accuracy requirements.
2) What we do is to use the drawing software to unfold this part, add thin plates in C, E and F, control the maximum gap after welding to 0.2 to 0.3 mm, before bending the sheet metal, use a manual beveling machine or The polisher removes excess matrix material, enabling precision machining of the part.
3) Description of the results.
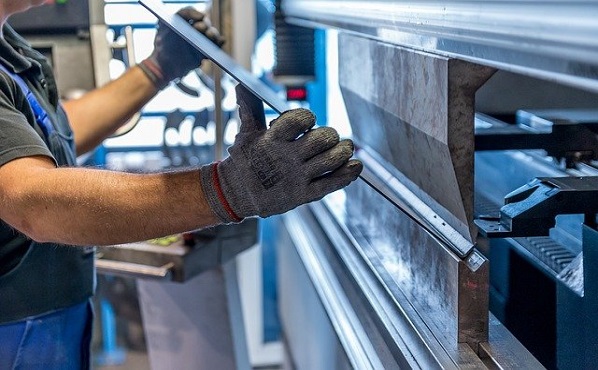
1. The round hole of the part process should be larger. In the food machinery industry, welding is not required, but it is more conducive to the cleaning of the machine.
2. Use a three-dimensional flexible platform to ensure the shape, position and dimensional accuracy of the workpiece, and use argon arc welding to bond the welding parts at multiple points. After the workpiece is fixed, you can take off the parts and complete free welding, which can effectively save time.
3. During welding, since the product gap is very small, it is not necessary to add welding wire, but to use self-melting method. After welding, the texture is beautiful, and no grinding is required. When shrinkage occurs, the parts are basically not deformed, and there is no need to increase the shaping process, and the technical requirements can be met at one time.
The above is the little knowledge of sheet metal processing. Do you want to know more about sheet metal processing? Platinum Shield will continue to give you more knowledge about sheet metal processing.