Material selection - For such large sheet metal parts, when material is inevitably wasted, we should consider folding it into several sub-parts, opening them for processing, and then welding them together, which not only guarantees Quality, but also reduce the waste of materials and save the old capital. Materials commonly used in sheet metal processing include cold rolled sheet (SPCC), galvanized sheet (SECC), copper sheet, aluminum sheet, stainless steel sheet, aluminum sheet, etc. Their functions are different. As for how to choose, we generally need to consider its function and old capital.
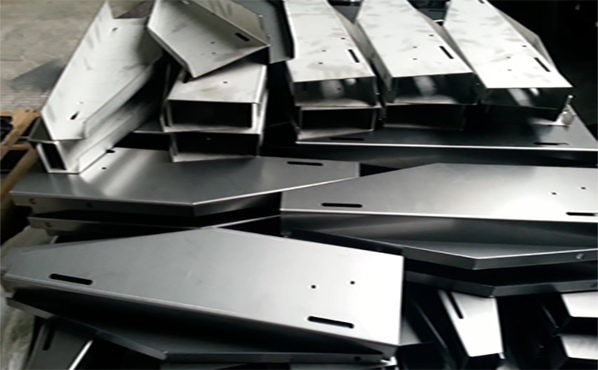
1. Cold rolled sheet is referred to as SPCC for appearance treatment. For electroplated colored zinc or painted parts.
2. Galvanized sheet is referred to as SECC, which is used for external treatment. This is the application of paint parts without special requirements. Generally, SPCC is used to reduce old capital.
3. Copper plate It is usually used for nickel plated or chrome plated parts and occasionally without penalty, depending on customer's requirements.
4. Aluminum sheets typically used for exterior treatments are chromate or oxide applications.
5. Stainless steel plate is divided into mirror stainless steel and matte stainless steel, it does not need to do anything.
6. Aluminium profiles typically used for exterior treatments are chromate or oxide applications, where it is important to play a supporting or continuous role. It is widely used in various plug-in boxes.
2. The process flow of sheet metal processing For any sheet metal part, there is a certain processing process, that is, the so-called process flow may vary with the layout of sheet metal parts, but generally does not span the following point.
1. Plan and draw part drawings of their sheet metal fabrication parts, also known as three views. Its function is to express the layout of sheet metal parts through drawing methods.
2 Draw an opening diagram, that is, open a complex part layout as a flat part.
3. There are many cutting methods for blanking, as follows:
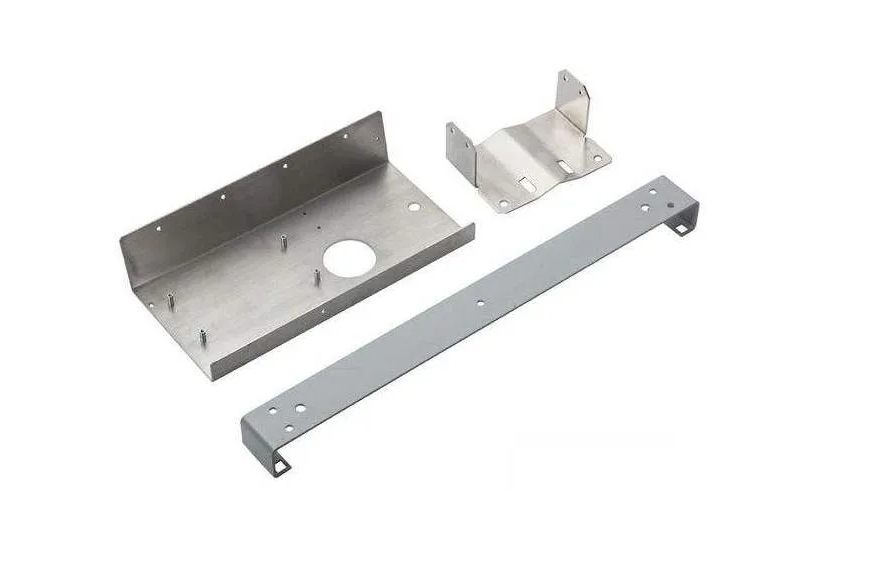
A. If the shearing machine has punching and chamfering, it is the total length and width dimensions of the opening drawing cut by the cutting machine, and the punch is turned to connect the punching and chamfering dies.
b. Punch blanking A punch is a layout for punching flat parts with a punch after opening the part in one or more steps. The advantages are short working hours and high compliance. CNC punching NC machining methods should be written at the beginning of CNC punching, i.e. using a programming application to compile the drawn opening diagram into an identifiable formula for the CNC machining machine, let it follow these French steps step by step on the iron plate, punching The layout style of the out part is its flat part.
d. Laser punching It is the layout style of cutting plane parts on iron plate by laser cutting method.
4. Flanging and tapping Flanging is also known as hole pulling, that is, draw a slightly larger hole on the smaller base hole, and then tap the hole. This increases its strength and avoids sliding teeth. Usually used for sheet metal processing with relatively thin plate thickness. When the plate thickness is larger, such as 2.0, 2.5 and above, we can simply tap without flanging.
5. Punching processing The hole can be processed by a common punching machine, and its processing requires a responsive mold to realize the operation. The punching convex shell has a convex shell mold, and the punching and tearing has a tear forming mold, etc. As far as our factory is concerned, pressure riveting studs, pressure riveting nuts, and pressure riveting screws are commonly used. The pressure riveting method is generally operated by a punch or hydraulic riveting machine, which is riveted to the sheet metal processing part.
7. Bending Bending is the folding of two-dimensional flat parts into three-dimensional parts, and its processing requires a folding machine and a responsive bending die to achieve operations, and has a certain bending sequence. The criterion is that if there is no interference, the next knife is folded first, and then folded after the interference.
8. Welding is the assembly and welding of multiple parts together for machining purposes, or the welding of edge seams on a single part to increase its strength. The processing methods are generally as follows: CO2 gas shielded welding, argon arc welding, spot welding, robot welding, etc. The choice of these welding methods usually depends on the actual requirements and materials. CO2 gas shielded welding is used for steel plate welding; argon arc welding is used for aluminum plate welding; robot welding is very important in the case of large materials and long welds, such as cabinet welding, robot welding Welding is acceptable, which saves many tasks and improves part-time compliance and welding quality.
9. Appearance treatment Appearance treatment generally includes phosphating film, electroplating color zinc, chromate, baking paint, oxidation, etc. Phosphating coatings are generally used for cold rolled sheets and electrolytic sheets. Its important function is to cover the surface of the material with a protective film to prevent oxidation; it can enhance the adhesion of baking paint, improve the appearance of cold-rolled sheets, and be used for electroplating colored zinc; chromates and oxides are often used in aluminum sheets and profiles. Appearance treatment; selection of detailed appearance penalty method is based on customer requirements.
10. Assembly The so-called assembly is to assemble multiple parts or components together according to a certain method, so that they become a complete material. In this process, we should pay attention to protect the materials and parts, do not scratch or bump the assembly is the last step to realize the materials and products. If materials and parts become unusable due to scratches and bumps, rework is required, which wastes a lot of machining time and adds to the old capital of materials and products. Therefore, pay special attention to the protection of materials and parts.
3. Sheet metal processing technology When processing sheet metal, you often encounter some problems. You need to optimize its process to make it a good product or achieve a specific goal. The following is a brief description of some process issues that we should always pay attention to when processing sheet metal.
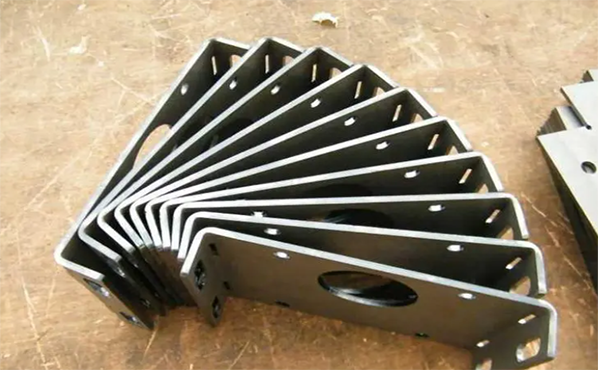
1. The processing of the door panel is usually to wrap the long side with the short side first, and then open the processing hole at the response corner. The size of the process hole is usually determined by the thickness of the sheet. When the thickness of the sheet increases, the size of the process hole should also increase accordingly, otherwise there will be edges and corners when bending.
2. Welded parts are typically positioned and welded using fixtures, holes or convex hulls. In some relatively difficult welds, convex hull or hole positioning is often used.
3. It can reduce the working time spent on positioning, ensure size, improve part-time compliance, and reduce old capital. For electroplated parts, since the electroplating solution has a corrosive effect on the material parts, it is generally necessary to add process holes at the corners of the electroplated parts to facilitate the real-time extrusion of the electroplating solution and ensure the quality.