In sheet metal design, as long as one dimension is miscalculated when drawing unfolds using traditional methods, the part may be scrapped after machining. However, designing with Pro/E is very easy. Just enter the exact bend radius without any sizing calculations. After clicking "Expand", the system will automatically expand for an accurate expanded view.
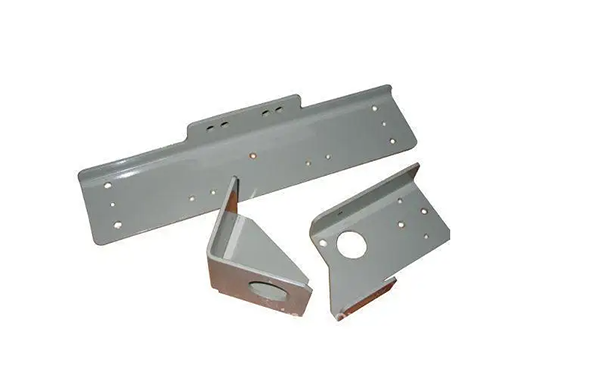
In Pro/E sheet metal design, the key factor affecting the dimensional accuracy of the unfolded drawing is the bending radius. Only by entering an accurate bending radius, the accurate unfolding size can be obtained. However, in the Pro/E Sheet Metal Module, there is no fixed formula for calculating the bend radius. Due to the different experience of designers, the dimensional accuracy of the unfolded drawing will produce different degrees of design errors. Even for important sheet metal parts with high precision requirements, some manufacturers prefer to use traditional methods to draw unfolds rather than the unfolds automatically generated by Pro/E. The traditional method of determining unrolled dimensions is usually to perform an experiment, bend the sample, measure the formed dimensions, and then compare the formed and blanked dimensions of the samples to obtain elongation. The nominal size minus the extension is the punched expanded size. Since the degree of elongation varies with the size of the bend fillet, manufacturers usually choose a uniform smaller fillet r<; the thickness of the sheet is uniformly extended, thereby simplifying manufacturing, according to the characteristics of the simple lines required for the sheet metal part. craft. If there are special requirements and different bending fillets must be used, the extension should be calculated separately, but this is rare in modern sheet metal manufacturing, such as CNC laser cutting machines, CNC bending machines, etc. CNC sheet metal processing equipment is widely used. Sheet metal processing technology has made a qualitative leap.
Traditional sheet metal part bending processing technology is characterized by extensive unfolding processing combined with mechanical cutting. First, lofting and blanking are carried out roughly according to the unfolded size, and bending is carried out after the subsequent machining allowance is reserved. Correct dimensions and machine holes after bending. This process has low requirements on the accuracy of the unfolded drawing, and has disadvantages such as complex process route, low efficiency, waste of materials, and difficulty in guaranteeing processing quality.
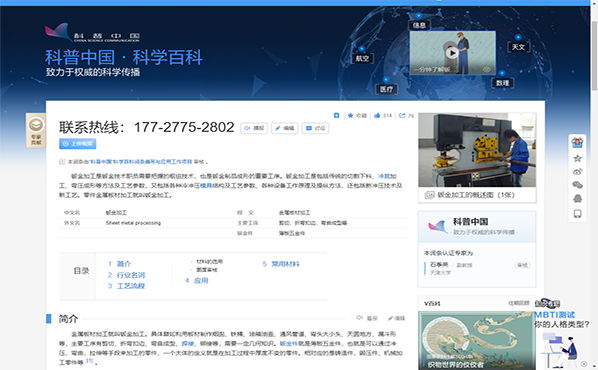
Modern bending sheet metal processing technology is characterized by unfolding processing and accurate part cutting. First, it is cut into shapes, holes and holes according to the unfolded drawing, and then bent to shape. This process has the advantages of closed-hole processing of sheet metal parts, simple process route, high efficiency and good processing quality, but it requires high precision for sheet metal unfolding. Therefore, in the modern bending sheet metal processing, the drawing of accurate unfolding becomes the primary problem to be solved.