In the development of sheet metal processing, sheet metal laser processing technology is increasingly emerging. Commonly used sheet metal laser processing technologies include: laser cutting technology, laser drilling technology and laser welding technology; let us introduce three common sheet metal laser processing technologies in detail.
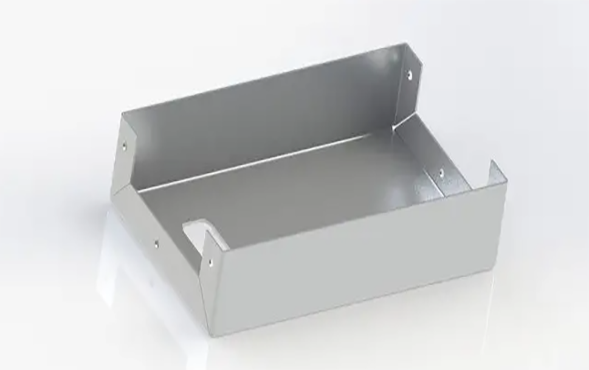
1. Laser Cutting Technology
Laser cutting machines have the characteristics of high flexibility, fast cutting speed, high production power, and short product production cycle, which have won a wide range of shopping malls for customers. This skill has a long lifespan. Most foreign plates with a thickness of more than 2 mm use laser cutting machines. Many foreign experts agree that the next 30-40 years will be the golden age for the development of laser processing technology
Laser cutting has excellent cutting function and precision, and the operation is very simple. Compared with mechanical cutting, it has the advantages of fast cutting speed, narrow cutting seam, high incision smoothness, small deformation, small heat-affected zone, and high power. Today, cutting is no longer limited to two-dimensional plane cutting, but prefers three-dimensional cutting.
Generally speaking, it is recommended to use a laser cutting machine to cut metal materials such as carbon steel plates within 12mm and stainless steel plates within 10mm. The laser cutting machine has no cutting force and no deformation. Whether it's a rough or messy part, it can be shaped and cut accurately and quickly with a laser in one go; good economics.
2. Laser Drilling Technology
Laser drilling is not only suitable for larger diameter circular holes, but also for smaller diameter circular holes. In some well-known laser drilling companies, small holes with a diameter of less than 0.2mm and a depth of 7mm can be processed.
The basic structure of laser drilling machine includes laser, foreman, cooling system, numerical control equipment and control panel. The foreman focuses the laser beam in the direction of the data processing hole. After the correct selection of processing parameters, the laser can be passed.
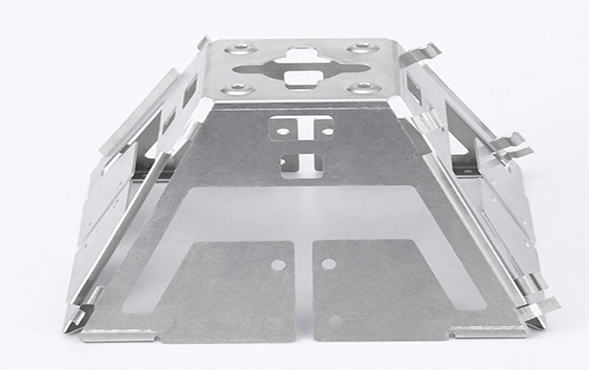
3 Light pulses are emitted to machine the desired holes. Laser welding technology Laser welding is an efficient and precise welding method with a high energy density laser beam as a heat source. Mainly used for welding thin-walled materials and low-speed welding. The welding process belongs to the heat conduction type, that is, the surface of the workpiece is heated by laser radiation, and the surface heat is dispersed in the interior through heat conduction. After controlling parameters such as laser pulse width, energy, peak power and repetition rate, the workpiece melts and forms a specific molten pool.
Laser welding can help us complete the welding of castings such as equipment. Many laser welds gradually reduce body weight with high quality and safety features. In addition, in China, the use of collaborative sheet metal processing skills has become a brave body processing skills.
Laser deep penetration welding usually chooses a continuous laser beam to complete the data connection. Its metallurgical physical process is very similar to electron beam welding, that is, the energy conversion mechanism is completed through the "pinhole" structure. When illuminated by a laser with a sufficiently high power density, the data diverges and small holes form. The vapor-filled hole acts like a black body, absorbing nearly all the energy of the incoming beam. The equilibrium temperature in the cavity reaches 25,000 degrees. Heat is transferred from the outer walls of the high temperature cavity to melt the metal surrounding the cavity.